Under normal circumstances, diameter + wall thickness are used, for example: diameter 57mm, wall thickness 3mm, wall thickness 3mm, we mark it as medium 57×3; we generally use the inner diameter of the pipe, which is commonly known as the nominal pressure inner diameter, for example: diameter 57mm , DN50, we mark it; we use feet, which are the inches often said on plumbing devices, for example: diameter 57mm, diameter 25.4mm, calculation of alloy pipe components: component per meter = (diameter wall thickness) x wall thickness x0.02491 (Enterprise: diameter and wall thickness are both mm, weight is Kg).
Welding process: heating the alloy pipe before welding, post-weld heat treatment, tempering, heating. Before welding the alloy pipe, the alloy pipe is mainly heated, and the welding starts after controlling the temperature for 30 minutes. Temperature control during the welding process and virtual beam temperature control solutions enable the automation of temperature control cabinets through temperature control solutions. The heat treatment equipment adopts far-infrared tracking board.
The intelligent control system automatically sets and records trend charts to accurately measure temperature and heat transfer coefficient. When the temperature rises, the distance between the heat transfer coefficient measurement point and the edge of the weld is 15-20 mm. Welding method, in order to avoid welding deformation of the alloy pipe, each column joint is welded symmetrically by two people, and the welding points are welded from the center to both sides. The welding seam is opened (the welding seam is opened close to the beam), and the operation process is from the beginning to the end – the third layer of the aluminum alloy pipe of the laminated pipe must be made to a minimum standard, because its welding key is to seriously affect the welding deformation. When welding one to three layers, planing must be performed. After the application of carbon arc gouging, the welding industrial equipment must be ground and polished, and the surface layer of the weld seam must be nitrided to make the surface metal shiny and avoid cracks caused by carbonization of the surface layer. Only the outer hole is welded, not the internal thread.
Electric welding = double-layer alloy pipe, the welding direction should correspond to the layer alloy seamless pipe, and so on. The spacing between butt welds in each layer is 15-20 mm. The welding current rate, welding speed and number of multi-layer stacks must be maintained for several powerful machines. When welding, you should start from the arc striking plate and then end with the arc striking plate. Sealing control, polishing and cleaning after welding. After heat treatment and electric welding, 12 hours of tempering should be carried out within 12 hours. If the heat treatment of the alloy pipe cannot be solved immediately, you should seek advice on heat insulation and slow cooling. When performing tempering treatment, the temperature values of the two heat transfer coefficients should be measured and welded on both sides.
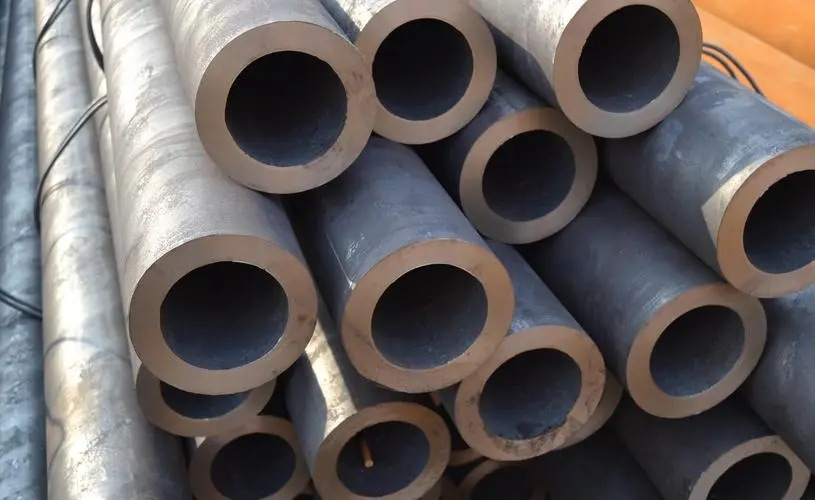
Similar Posts
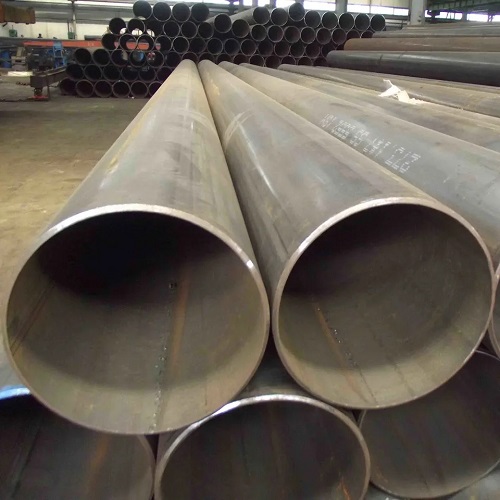
Classification of welded steel pipes
Welded steel pipes are made of steel plates or strips. Welded steel pipes are divided into furnace welded pipes, electric…
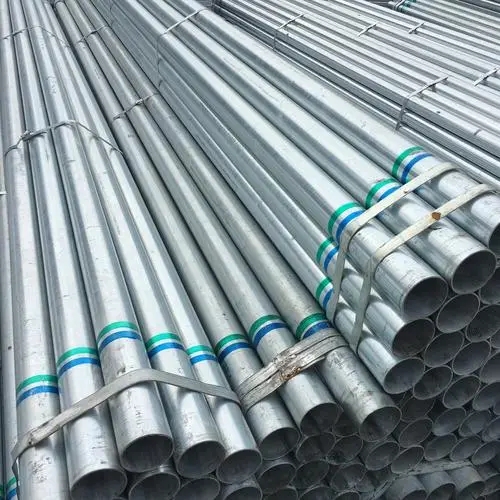
The difference between hot-dip galvanized steel pipe and cold-dip galvanized steel pipe
The corrosion resistance of hot-dip galvanized steel pipe is dozens of times that of cold-dip galvanized steel pipe. Let’s take…
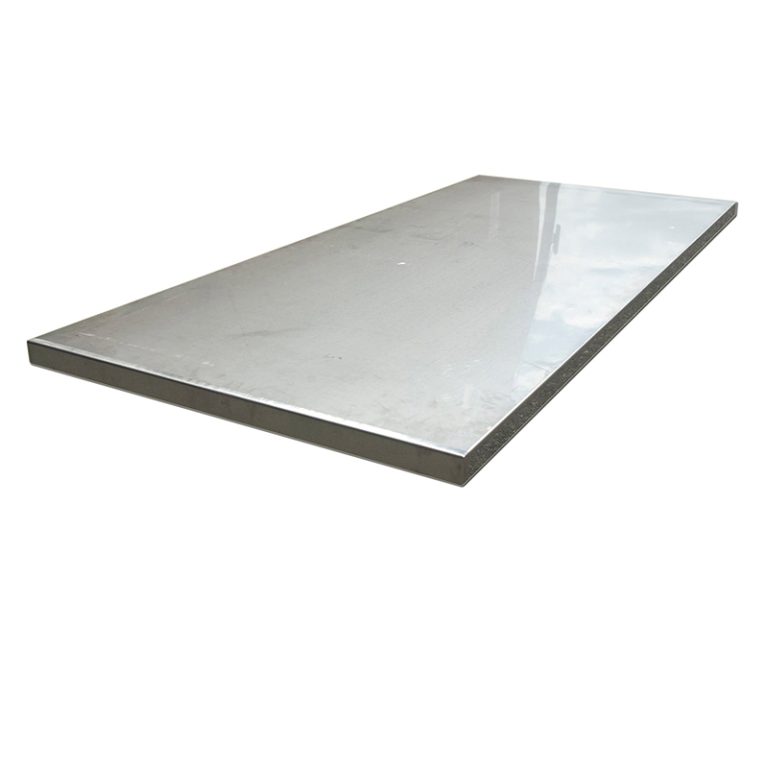
Uses of 316L stainless steel plate
The advantages of 316L stainless steel include excellent corrosion resistance, especially in chloride environments; good weldability and formability; high temperature…
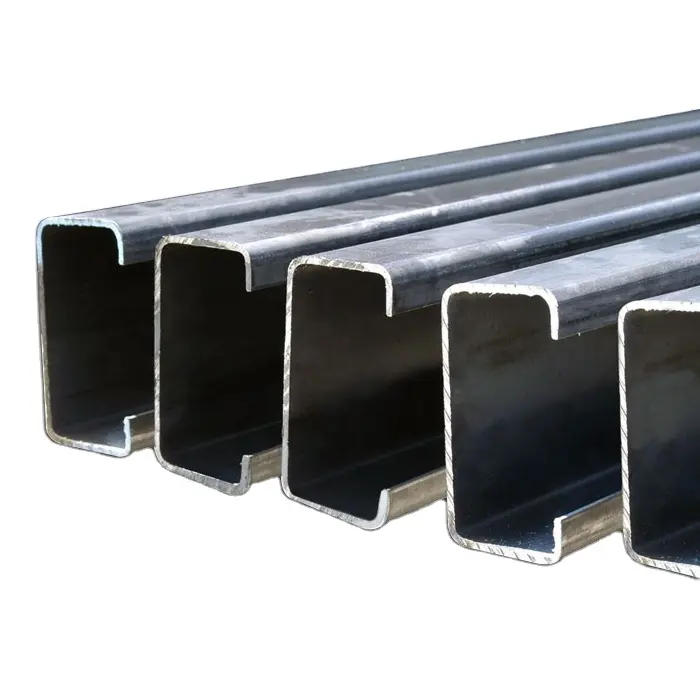
What is the difference between channel steel and C-shaped steel?
Speaking of C-shaped steel, we have to think of channel steel. Why is this? The reason is that C-shaped steel…
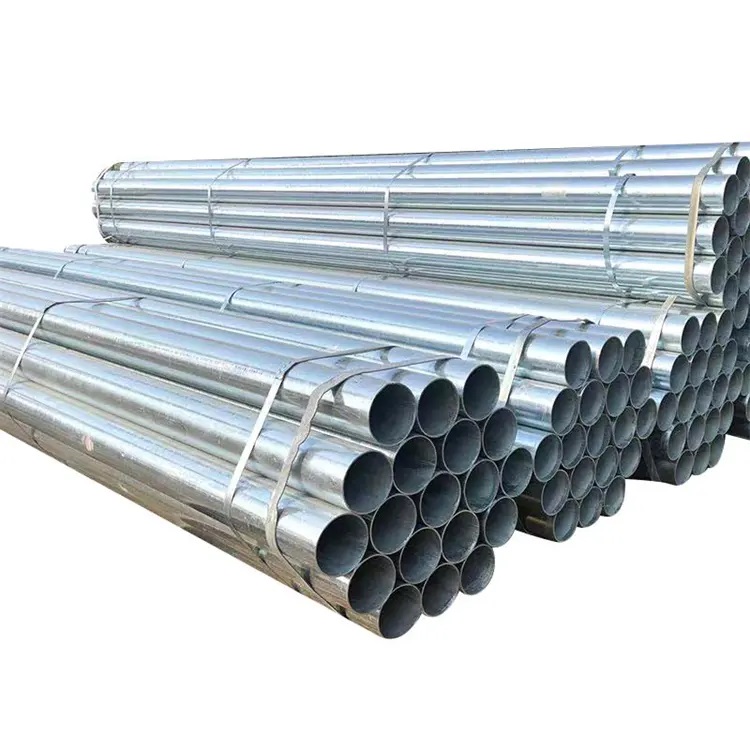
What are the benefits of stainless steel pipes over galvanized pipes?
Stainless steel pipes have many advantages over galvanized pipes, especially in certain applications and environments. Here are some of the…
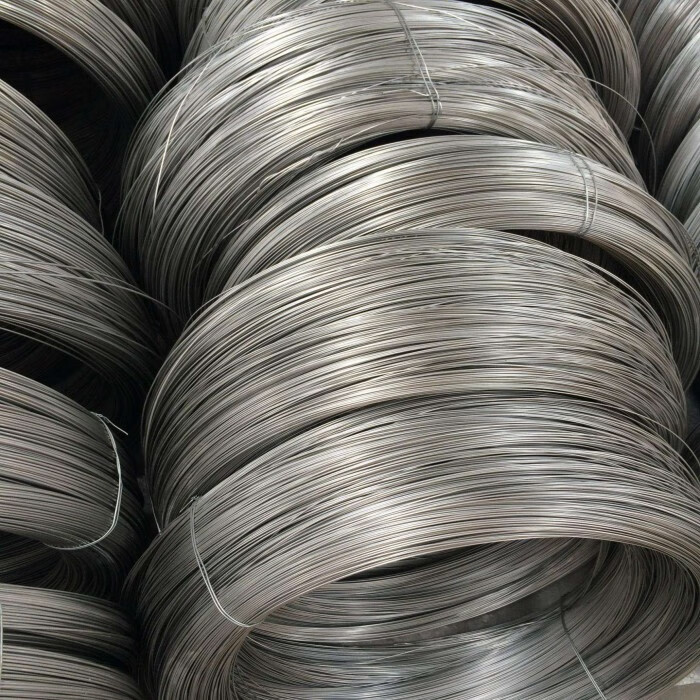
What coatings can stainless steel wire have?
Stainless steel wire can be treated with a variety of coatings or plating to improve its properties, such as corrosion…
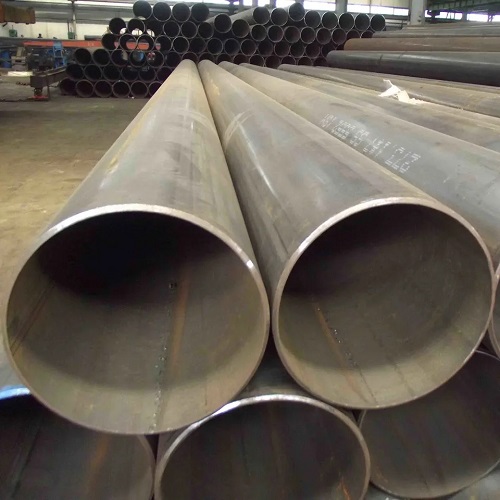
Classification of welded steel pipes
Welded steel pipes are made of steel plates or strips. Welded steel pipes are divided into furnace welded pipes, electric…
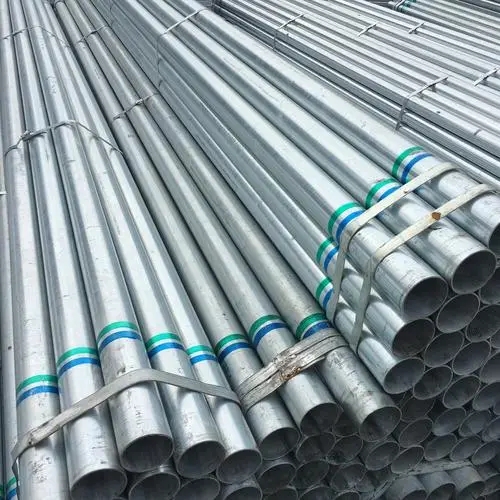
The difference between hot-dip galvanized steel pipe and cold-dip galvanized steel pipe
The corrosion resistance of hot-dip galvanized steel pipe is dozens of times that of cold-dip galvanized steel pipe. Let’s take…
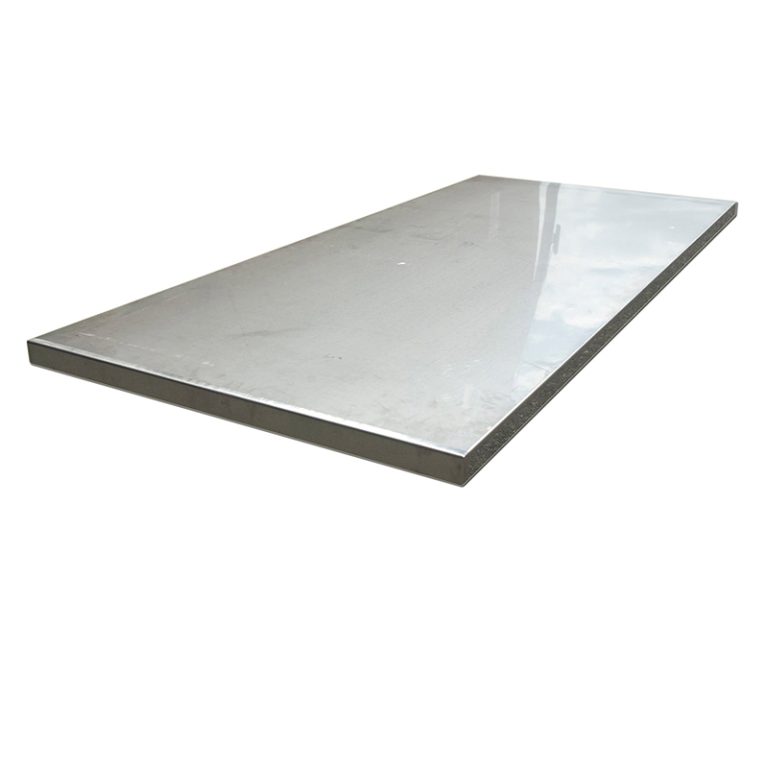
Uses of 316L stainless steel plate
The advantages of 316L stainless steel include excellent corrosion resistance, especially in chloride environments; good weldability and formability; high temperature…
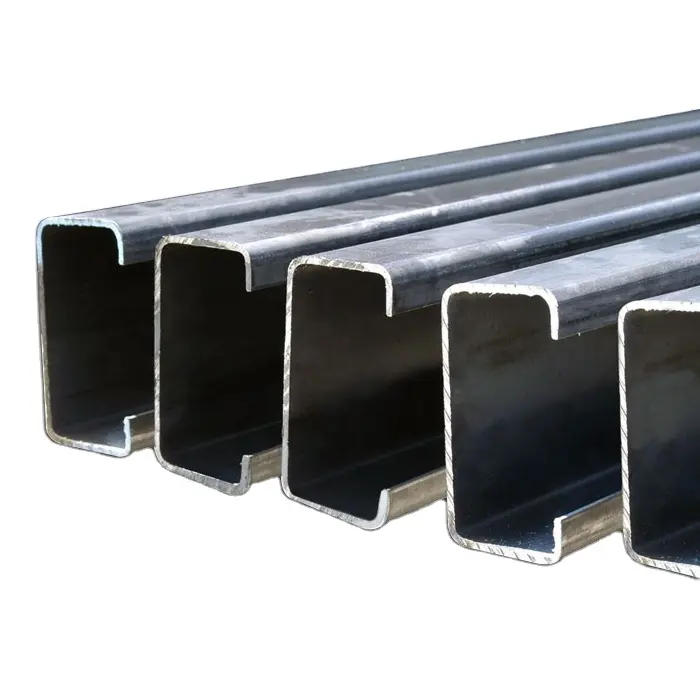
What is the difference between channel steel and C-shaped steel?
Speaking of C-shaped steel, we have to think of channel steel. Why is this? The reason is that C-shaped steel…
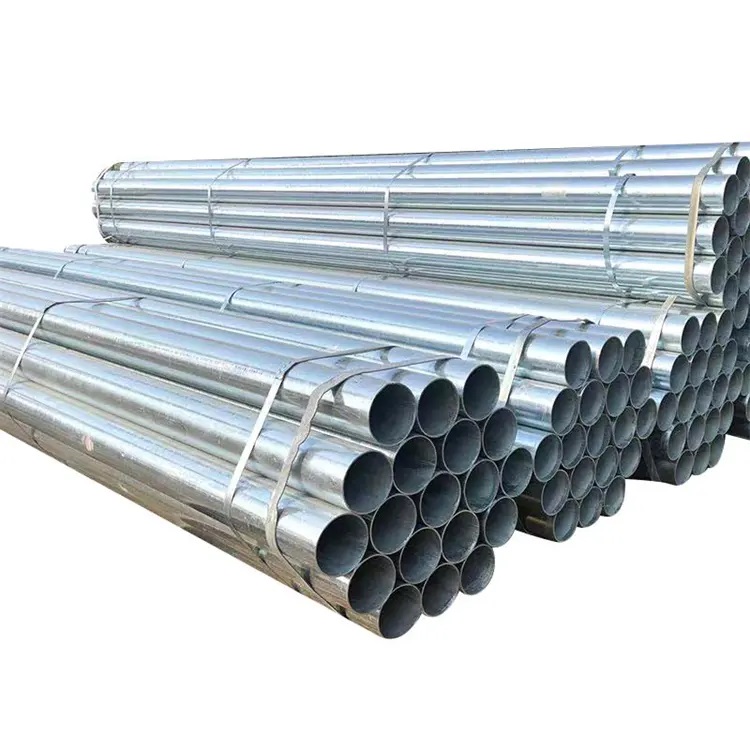
What are the benefits of stainless steel pipes over galvanized pipes?
Stainless steel pipes have many advantages over galvanized pipes, especially in certain applications and environments. Here are some of the…
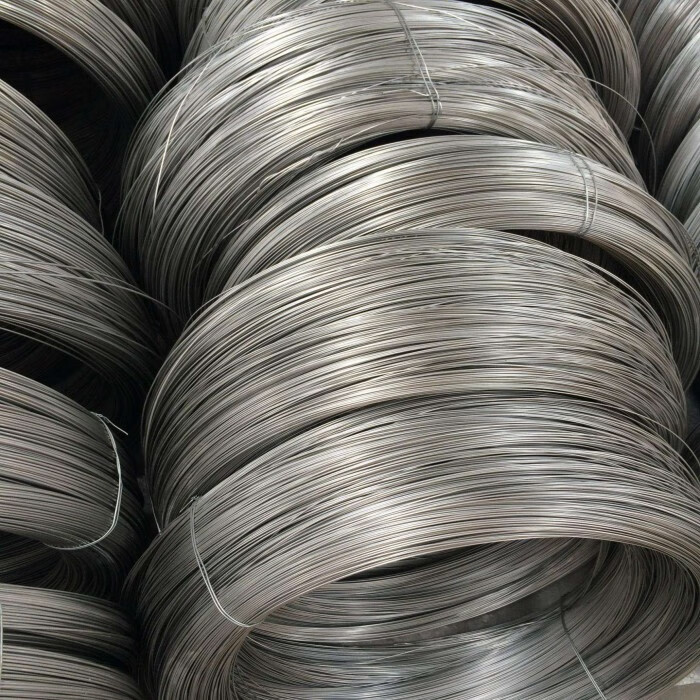
What coatings can stainless steel wire have?
Stainless steel wire can be treated with a variety of coatings or plating to improve its properties, such as corrosion…
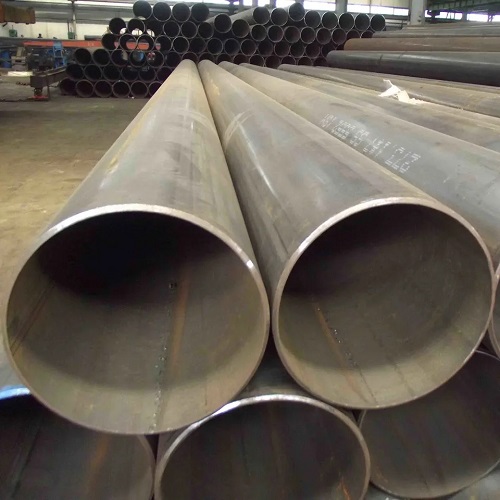
Classification of welded steel pipes
Welded steel pipes are made of steel plates or strips. Welded steel pipes are divided into furnace welded pipes, electric…
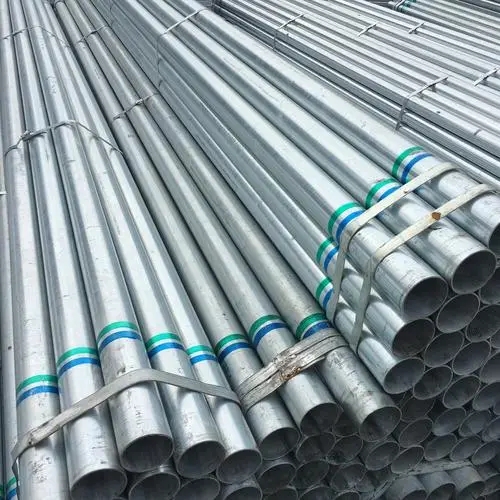
The difference between hot-dip galvanized steel pipe and cold-dip galvanized steel pipe
The corrosion resistance of hot-dip galvanized steel pipe is dozens of times that of cold-dip galvanized steel pipe. Let’s take…
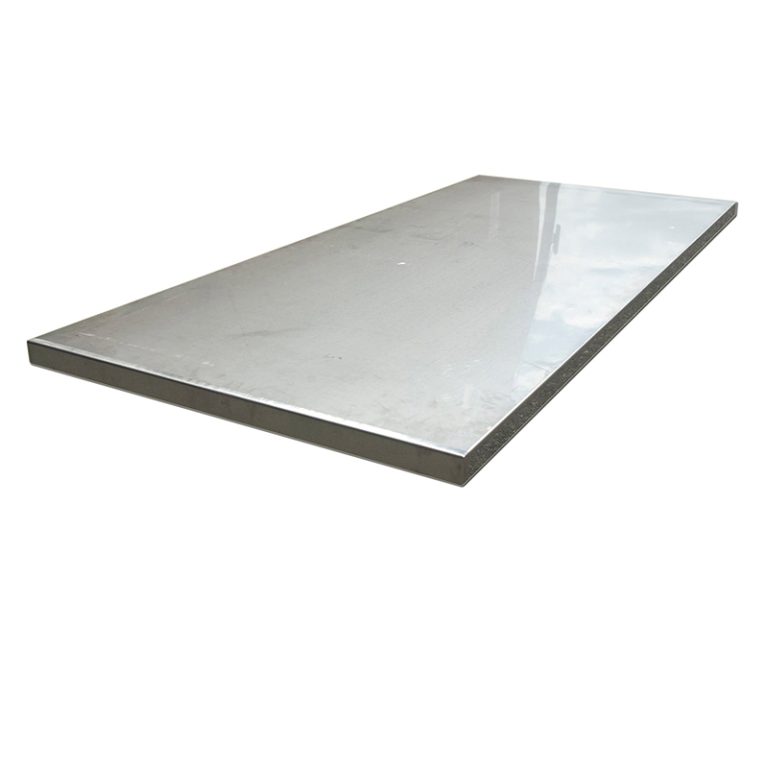
Uses of 316L stainless steel plate
The advantages of 316L stainless steel include excellent corrosion resistance, especially in chloride environments; good weldability and formability; high temperature…
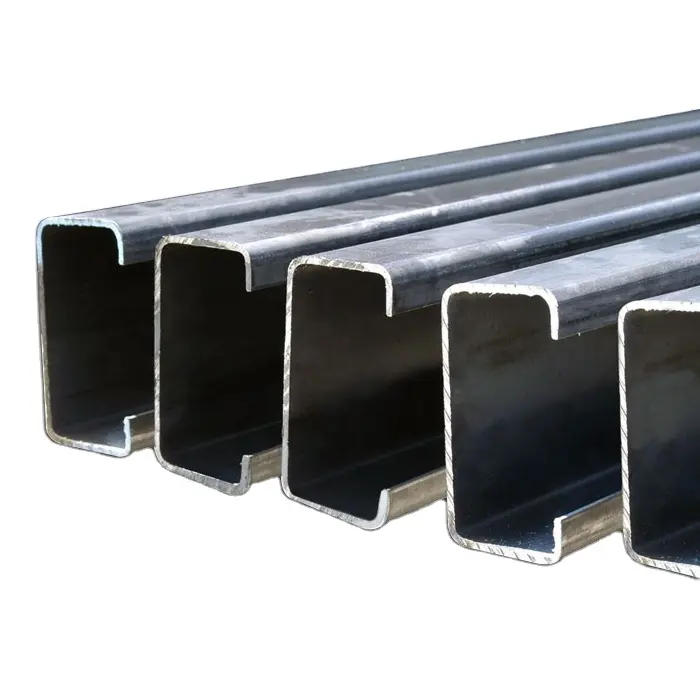
What is the difference between channel steel and C-shaped steel?
Speaking of C-shaped steel, we have to think of channel steel. Why is this? The reason is that C-shaped steel…
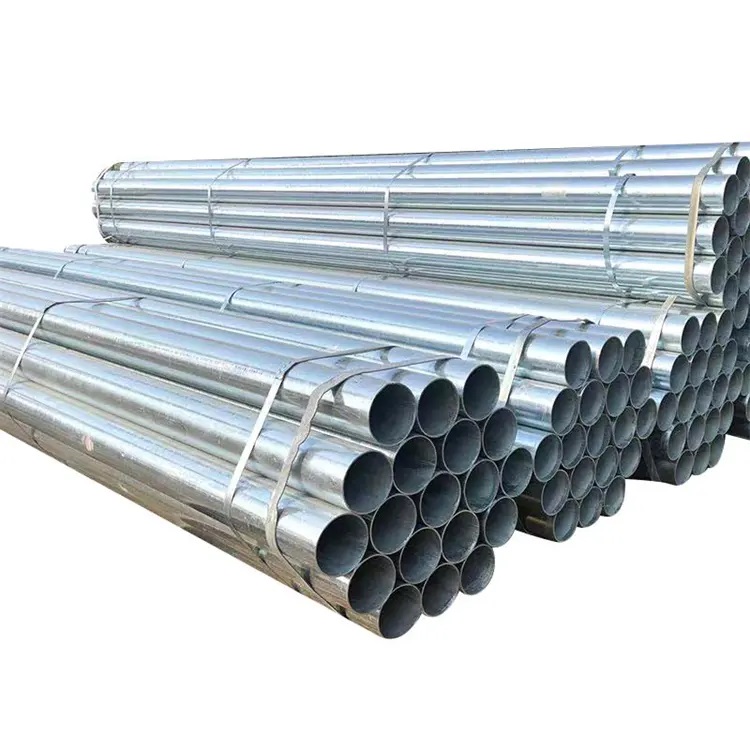
What are the benefits of stainless steel pipes over galvanized pipes?
Stainless steel pipes have many advantages over galvanized pipes, especially in certain applications and environments. Here are some of the…
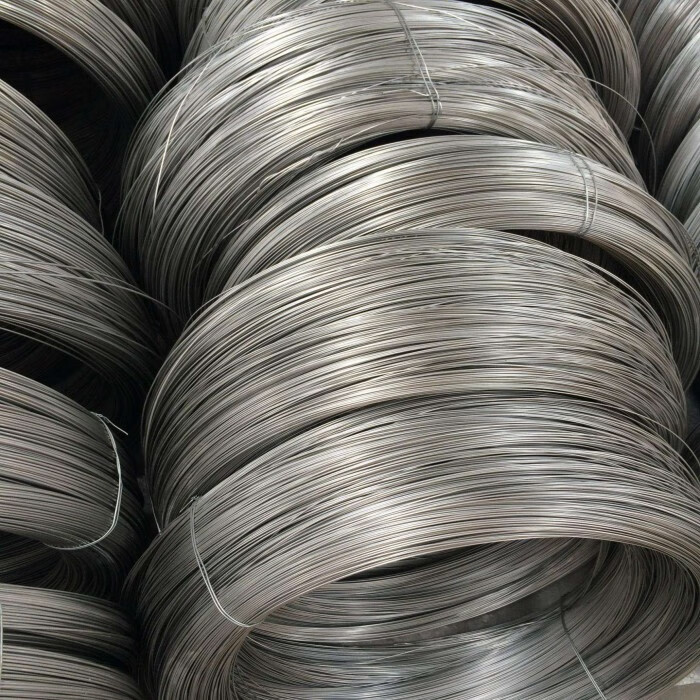
What coatings can stainless steel wire have?
Stainless steel wire can be treated with a variety of coatings or plating to improve its properties, such as corrosion…